Ensuring the reliability and accuracy of processes and equipment is paramount In scientific research and manufacturing, Two key concepts that play a crucial role in this assurance are qualification and validation. While these terms are often used interchangeably, they signify different procedures with unique purposes and methods. Qualification and validation are crucial processes in various industries, especially those involving R&D, manufacturing, and regulated sectors such as Pharmaceutical or Biotechnological.
Qualification
Qualification refers to a systematic and documented process of evaluating and verifying the capabilities of a system, equipment, process, or facility to ensure that it meets predefined requirements and specifications. The goal of the qualification is to demonstrate that the subject under consideration is suitable for its intended purpose and operates within established parameters. The qualification process typically involves stages such as Installation Qualification (IQ), Operational Qualification (OQ), and Performance Qualification (PQ), each one focusing on specific aspects of the system or equipment to ensure its proper installation, functioning, and consistent performance. Qualification is commonly employed in industries such as pharmaceuticals, biotechnological, or manufacturing, to maintain the reliability and integrity of processes and products.
Key Components of Qualification:
- Installation Qualification (IQ): This initial phase verifies that the equipment or system is installed correctly and in accordance with the manufacturer's specifications. It involves checking physical attributes, such as location, power supply, and environmental conditions.
- Operational Qualification (OQ): OQ focuses on assessing whether the equipment or system operates within specified parameters. This involves testing under normal operating conditions to ensure that it functions as intended.
- Performance Qualification (PQ): PQ is the final stage of qualification, evaluating the system's performance in its intended environment. This phase aims to confirm that the equipment consistently produces results meeting predefined acceptance criteria.
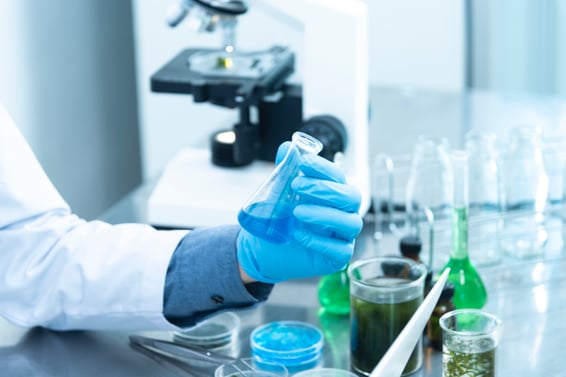
Validation
Validation, on the other hand, is a broader and more complex process that extends beyond the assessment of equipment and encompasses the evaluation of the entire process. Validation ensures that a process consistently produces results meeting predetermined specifications, leading to the production of reliable and high-quality products or services. It is particularly crucial in industries like pharmaceuticals throughout the whole pipeline from the preclinical process to the post-marketing, once the product is being commercialized to ensure the quality of the product or process.
Key Components of Validation:
- Prospective Validation: Conducted before routine production or assay performance, prospective validation involves establishing documented evidence that a process will consistently produce the desired results.
- Retrospective Validation: This form of validation is performed using historical data to confirm the consistency of a process over time. It is particularly useful when a process has been in operation for an extended period.
- Concurrent Validation: In cases where immediate production is necessary, concurrent validation is employed. This involves collecting and assessing data in real-time during actual production.
Qualification vs Validation
While both qualification and validation aim to ensure the reliability of processes and assays, the key distinctions lie in their scope and focus. Qualification primarily evaluates the fitness of equipment, systems, or models, ensuring they meet predetermined specifications. Validation, on the other hand, is a broader process that assesses the entire production method or assay, ensuring consistent and reliable results over time.
In conclusion, qualification and validation are indispensable components of quality assurance in scientific research and manufacturing. Understanding the differences between these processes is essential for researchers, engineers, and professionals in various industries to implement effective quality control measures. By employing a systematic approach to qualification and validation, organizations can enhance the robustness of their processes, adhere to regulatory standards, and ultimately deliver high-quality products and outcomes.
References
- Aljurf, M. et al. (2021) ‘Qualification and Validation’, in Quality Management and Accreditation in Hematopoietic Stem Cell Transplantation and Cellular Therapy. Switzerland: Springer International Publishing AG.
- Kauffman, J. S. (2005) Qualification and Validation of USP Apparatus 4. Dissolution technologies. [Online] 12 (2), 41–43.
- EudraLex. Volume 4. EU guidelines for good manufacturing practice for medicinal products for human and veterinary use Annex 15: qualification and validation. http://academy.gmp-compliance.org/guidemgr/files/2015-10_annex15.pdf.
- EudraLex. The rules governing medicinal products in the European Union. Volume 4. Good manufacturing practice medicinal products for human and veterinary use Annex 11: computerized systems. http://academy.gmp-compliance.org/guidemgr/files/annex11_01-2011_en.pdf.